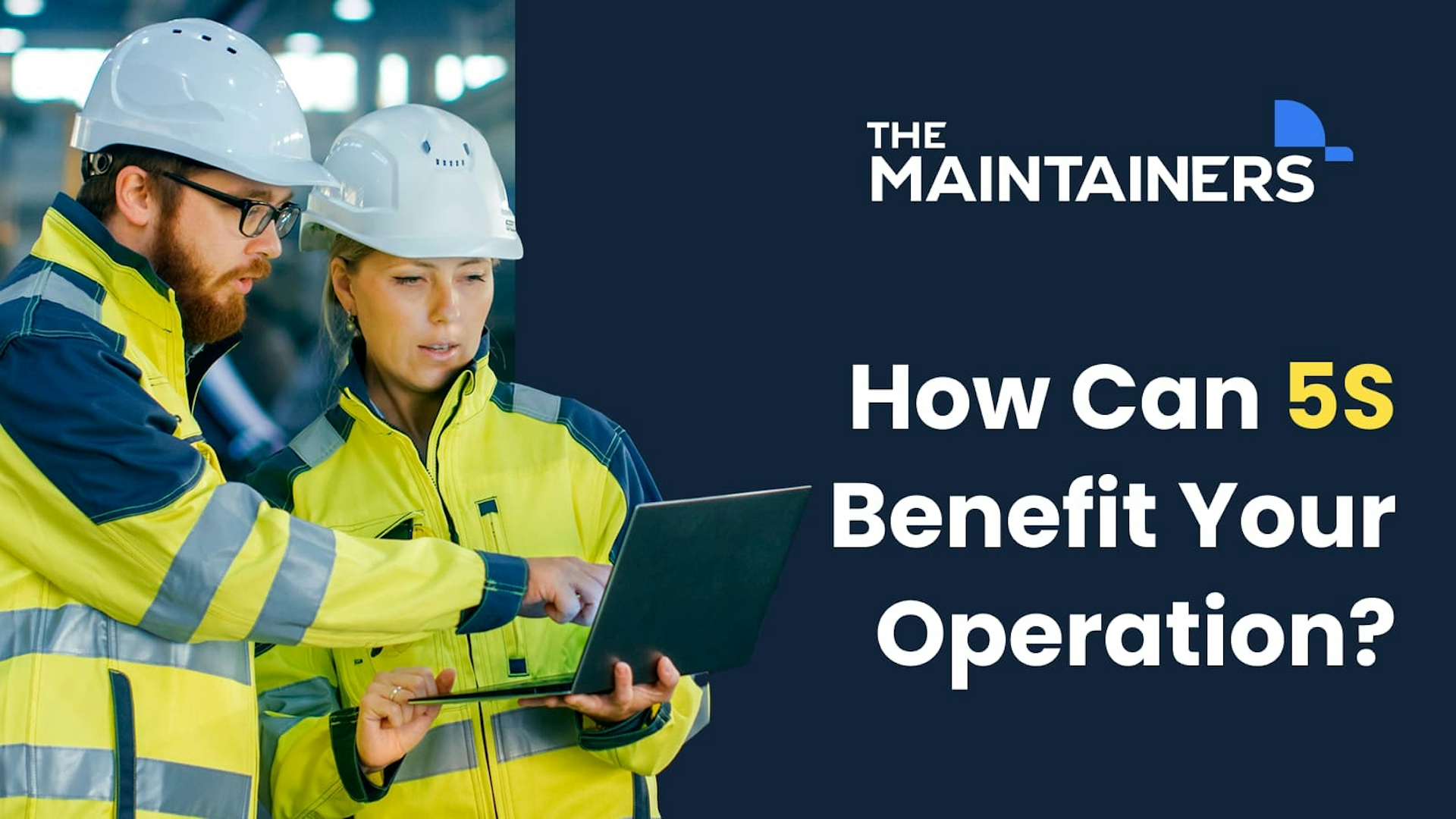
Implementing 5s Methods To Improve Your Production
By The Maintainers • January 17, 2024
The 5S methodology is a systematic approach to workplace organization and visual management, originating from Japanese manufacturing practices. Comprising five core principles, each beginning with the letter ‘S,’ 5S stands for Seiri (整理), Seiton (整頓), Seiso (清掃), Seiketsu (清潔), Shitsuke (躾).
In English, these translate to Sort, Set in Order, Shine, Standardize, and Sustain.
The 5S methodology is often attributed to the Japanese manufacturing sector, particularly to the Toyota Production System (TPS). While the specific inventor or originator is not clearly defined, 5S principles emerged as a part of the broader Lean manufacturing philosophy and continuous improvement practices pioneered by Toyota.
The 5S methodology consists of five fundamental principles, each beginning with the letter ‘S’:
- Sort (Seiri):
In this initial step, the focus is on eliminating unnecessary items from the workplace. This involves a critical evaluation of tools, materials, and equipment, retaining only what is essential for daily operations.
- Set in Order (Seiton):
Once the unnecessary items are removed, the next step involves organizing the remaining items in a systematic and efficient manner. This includes defining specific locations for tools, labeling, and ensuring easy accessibility.
- Shine (Seiso):
Maintaining a clean and organized workspace is integral to the 5S philosophy. Regular cleaning activities not only enhance visual management but also contribute to a safer and more pleasant work environment.
- Standardize (Seiketsu):
Standardization involves creating uniform processes and procedures for maintaining the first three S’s. It ensures that the improvements made are sustained over time, promoting consistency and stability in operations.
- Sustain (Shitsuke):
The final S focuses on creating a culture of continuous improvement. Sustaining the gains achieved through the previous steps involves ongoing training, regular audits, and fostering a mindset of continuous refinement.
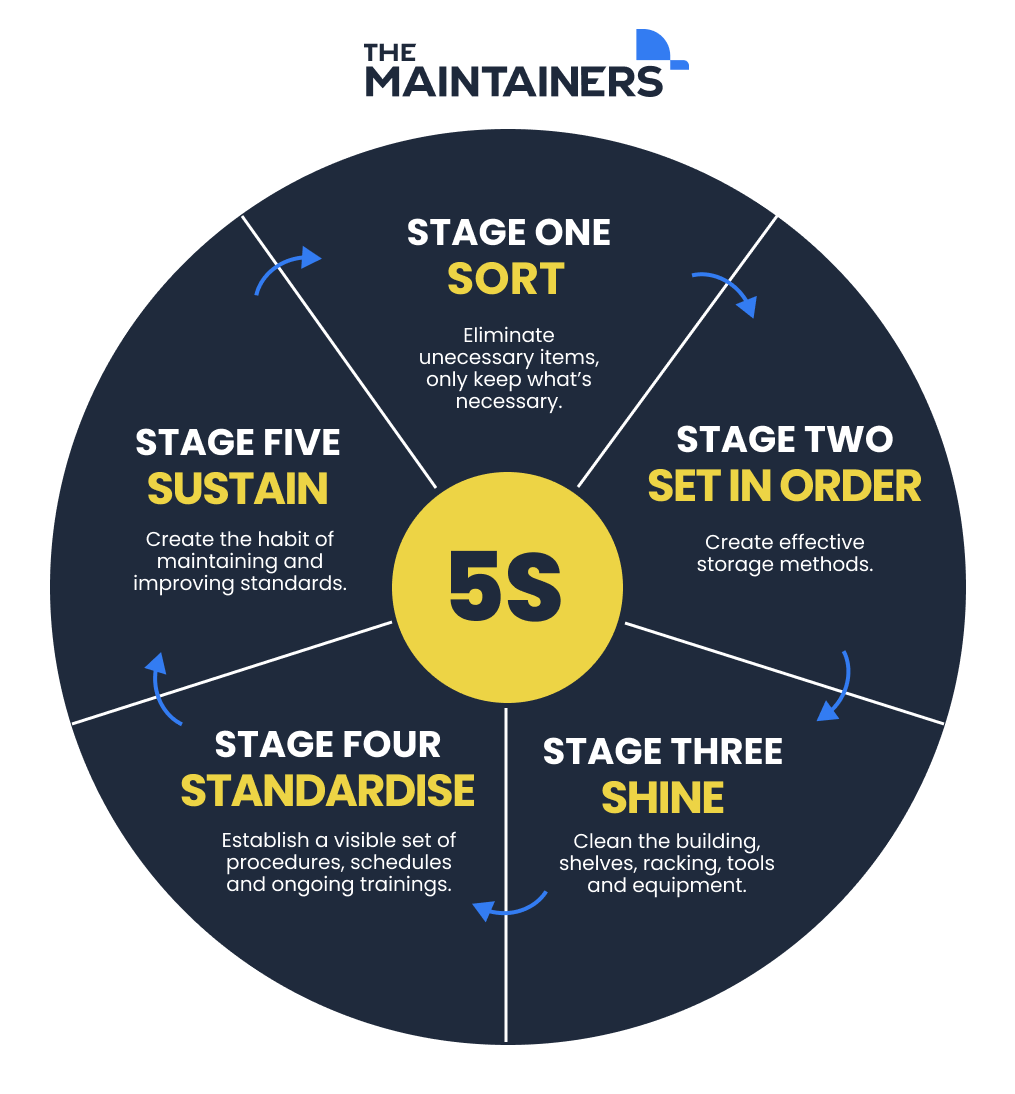
Why Implement the 5s?
Implementing the 5S methodology in your production process can yield substantial benefits, significantly enhancing efficiency and overall operational performance. Firstly, the “Sort” step ensures that your workspace is decluttered and only essential items are retained, eliminating unnecessary distractions and reducing the risk of errors. This leads to a more organized and focused work environment. The “Set in Order” principle facilitates a systematic arrangement of tools and materials, optimizing accessibility and minimizing time wasted on searching for items. This, in turn, streamlines workflows, leading to increased productivity.
The “Shine” aspect emphasizes cleanliness and regular maintenance, creating a work environment that is not only aesthetically pleasing but also promotes employee health and safety. A clean and well-maintained workspace can contribute to higher morale and a sense of pride among workers. The “Standardize” step establishes consistent processes and procedures, reducing variability and improving overall quality control. Standardization also facilitates easier training of new employees, ensuring that everyone follows the same best practices.
Lastly, the “Sustain” phase focuses on embedding the 5S principles into the organizational culture, fostering a continuous commitment to improvement. This long-term commitment results in a workplace that is not only more efficient but also adaptable to changes and challenges.
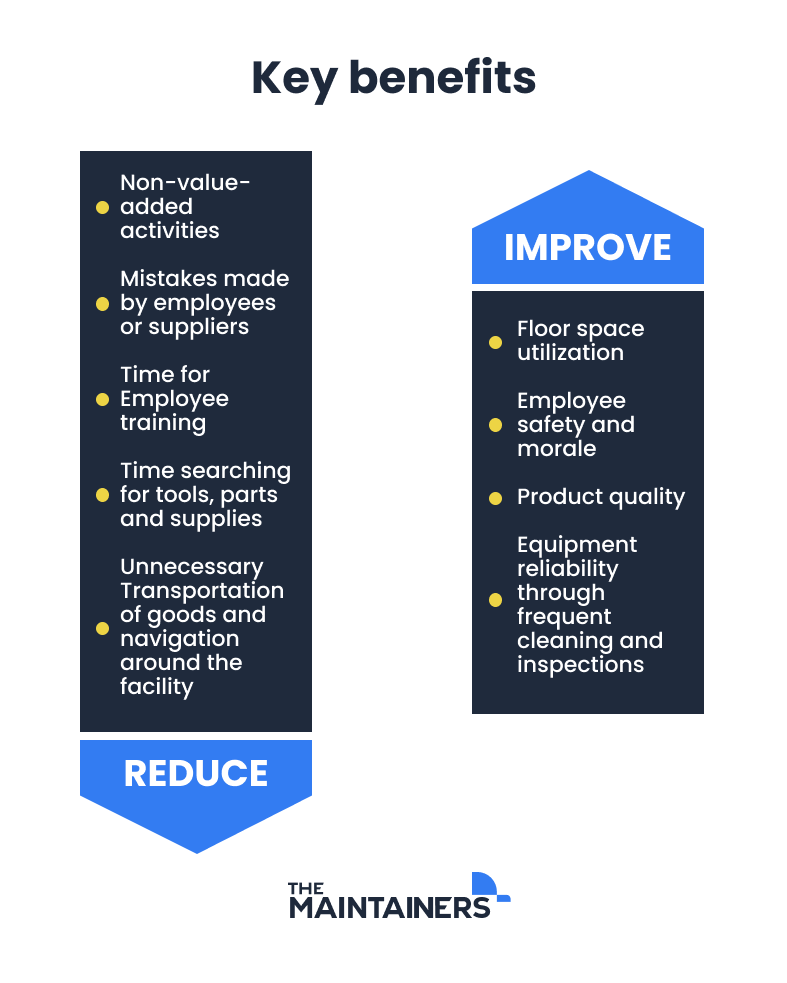
How Does 5s Relate to Lean?
The 5S methodology and Lean principles share common ground as both are rooted in Japanese manufacturing philosophies, aiming for efficiency, waste reduction, and continuous improvement. However, they are distinct in their focus and scope.
5S is primarily concerned with organizing the workplace, minimizing waste, and creating a structured and efficient environment. The focus is on visual management, cleanliness, and establishing standardized processes.
On the other hand, Lean manufacturing, often referred to as simply “Lean,” is a broader philosophy that encompasses various principles and practices aimed at reducing waste, improving efficiency, and delivering value to customers. Lean thinking goes beyond the physical organization of the workplace and includes concepts such as just-in-time production, continuous improvement (Kaizen), and respect for people. Lean aims to create a culture of continuous improvement throughout the entire organization, involving employees at all levels.
While 5S is a specific methodology focused on workplace organization and standardization, Lean is a broader philosophy that incorporates a range of principles, tools, and practices with the overarching goal of creating a more efficient and value-driven organization. 5S can be considered a subset or foundational element within the broader framework of Lean manufacturing.